images of living room chairs
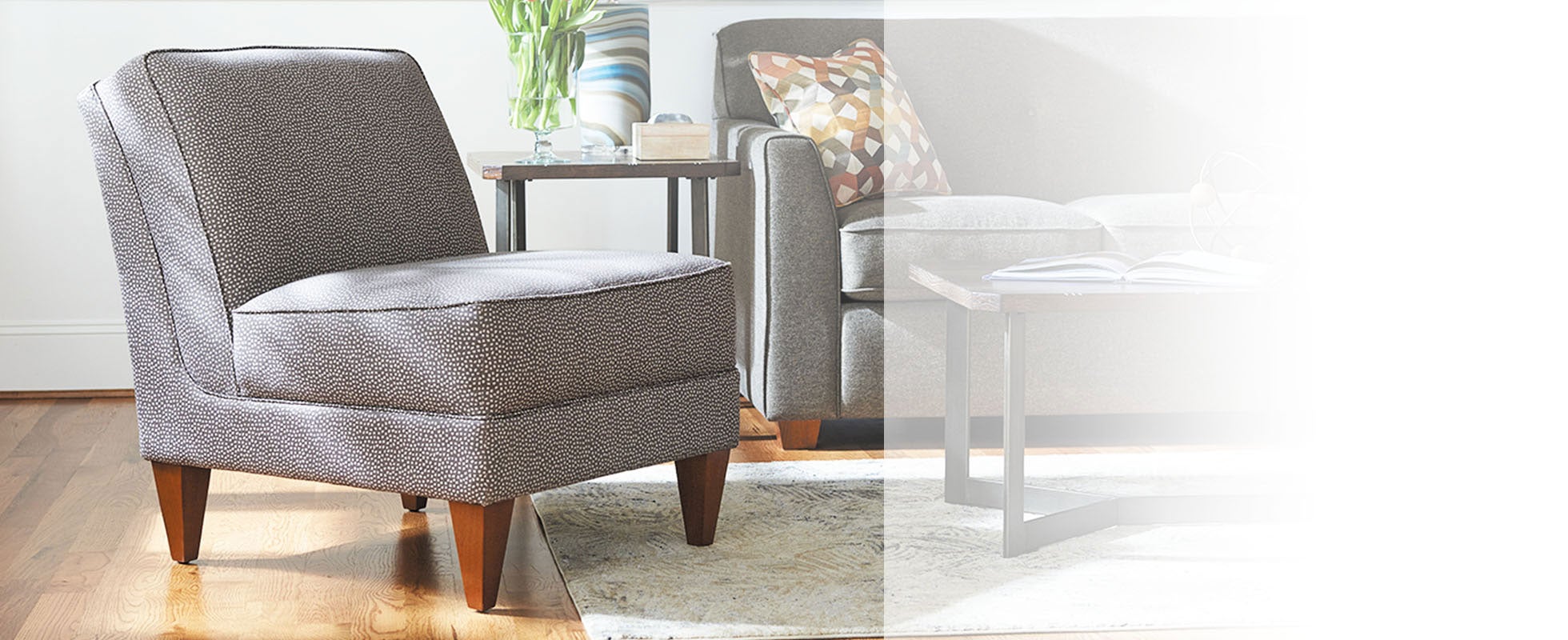
voiceover:the woodwhisperer is sponsored by powermatic and clear vue cyclones. marc:see this right here? that's the blacker house chair. i'm going to show you how i made it. (lively music) the blacker house chairwas originally built for the blacker housein pasadena california, that was back in 1907.
it's a very complex chair and it's been on mybucket list for years now and i'll show you some of thedetails and you'll see why. the back consists of bent laminated slats and features of beautiful string inlay. the back legs curve backwards while also flaring out to the sides. the arms are not only curved but tapered in thicknessand joined up to the legs
via long ebony splines. in traditional greene and greene fashion, there are ebony plugs everywhere including in the sculpted crest rail. brackets adorn the frontleg to rail joints. the bottom rail features asmall angled through tenon and each leg is given theclassic greene and greene indent detail. even if you don't like thegreene and greene style,
you have to respect the craftsmanship. now to build a chairlike this from scratch we take an insane amount of time just developing the templates, getting all the measurements right, building prototypes, testing them and then going back andbuilding more prototypes. it's just something that unfortunately with my current schedule,
there's no way that i coulddevote that much time to it. i went to the william ng school. it's one of the only placesin the country that you can go to learn how to build this chair and william has the processdown to its science. all the jigs are there. all the templates are there and you have the toolsthat you need to make it. it's the only way you can doit in that period of time.
even then i still hadto bring this puppy home and do the final assemblyand all the finishing touches here in my shop. it's quite an endeavor but doing it this way was the only way that i could get it done. all right, now you'll have toforgive some of the filming that i did for this because iwas busy building the chair. i didn't get to document every last detail
like i normally would but i still wanted to take the opportunity to bring you on the journey of building such a complex andamazing piece of furniture. let's head out to anaheim, california where the william ng school is located and i'll show you how i built it. the eight day class started with a review of the full size plans
and then we got right towork with the sapele wood, a species very similar to mahogany. first up are the front legs. these legs are unique and that they're shaped like a rhombus. we need to make a couple ofbevel cuts at the table saw. we cut one side and thenflip the piece around to make the second cut on the other side. you're going to see a lot of this bad boy,
the jds multi-router. it was introduced back in 1987 and woodworkers everywhere had been pining for them ever since but with the price tag of nearly $3,000, it's out of most woodworker's budgets. as you can see it makes quickwork of these angled mortises. we were also able to make the leg indents with the help of a positioning jig
and speaking of jigs, thisproject has a lot of them. now the back legs need to be cut to shape in two dimensions and a template provides the guidelines. a quick bandsaw cut removesthe bulk in one dimension and then we'll use a jig and a pattern bit to bring the leg to its final shape. the bit isn't tall enoughto do the work in one pass so a second pass is donewith a different bit
using the first section as a guide. before cutting the length to final shape, we need to cut slats for splines. this is the spline thatholds the crest rail to the top of the back legs. (mellow music) now here's a look at thelegs after final shaping. now it's time for the arms. the shape is traced on using a template
and then rough cut at the bandsaw. just like the legs, the arms are rounded to final shape using a pattern bit. the arms were intentionally cut long so that we'd have an extrachunk of material leftover. that piece is flipped to the underside and glued in place giving us the additional thickness we need with a near perfect greene match.
the arms now need ataper from front to back so we use a special setof jigs at the bandsaw. just like that, the arms take shape. now it's time for a little dry assembly. with the parts secured in place, the arms are scribed into the back legs for a nice step notch. a router is used to remove the bulk and a chisel does the rest.
the end result is a verystrong arm to leg connection that will be reinforcedwith a screw later. the arms now need to be cut to final shape using the bandsaw. the profile is sanded until it matches up with the front legs perfectly. now that's what i'm talking about. using another carriage jig, the arms and legs are held in place
while we use a slat cuttingbit to create the grooves for the ebony splines. we'll need a groove inthe front and in the back. the bent laminated back slats are made by re-sawingstack into thin sheets. glue is then applied to each strip and the stack is clampedto a bending form. for best results, usea butt ton of clamps. the next day, the laminationcomes out of the form
and appears as one piece of wood. the shape of the back slots is traced on and the pieces are cut at the bandsaw. the through mortises for the bottom rail need to be clean and crisp so we use the hollow chiselmortiser to make them. after the angle tendon is cut, it protrudes just slightlythrough the mortise. after cutting the mortisesin the crest rail,
we use the table saw to makethe appropriate bevel cut. this is where thingsget pretty complicated. the slat for the splines hasto be routed in two steps and at the perfect angle. with the help of a positioning jig, pneumatic clamps, and the multi-router, the results are as perfect as they can be. now we can finesse thefit of the back slats. the slats need to besnug but not too tight.
to give the crest rail its unique profile, we'll use power carving tools. the crest rail is made to look as if it's folding over almost like a wave so there's a lot of material to remove. a rasp does a final finesse work and a random orbit sander makeseverything nice and smooth. the center back slack getssome extra decorative elements like these square holescut at the scroll saw
and a beautiful string inlay design. the template is glued right to the slat and a small router bit isused to cut the grooves. thin strips of mapleare soaked in hot water and are gently driven intothe slats with a hammer. believe it or not we'reat day eight at this point and it's time to head home. back in my own shop i proceedwith the final details. ebony plug holes are cutusing lee valley hole punches.
the ebony splines are dryfit and cut to rough shape. to simplify the assembly, i glue some splines in ahead of time, and then assemble each sideof the chair separately and then install the armsand associate its splines. now it can bring thetwo chair sides together with the front and back rails. epoxy gives me the extraworking time that i need to get this glue up perfect.
clamps were then added with the help of custom angled [claws]. the back slats are nowdropped into the back rail. the tricky part gettingthe crest rail aligned with five separate mortises. now for the splines, as you can see they're still over-sized. we'll trim them to size after assembly. just a little downwardpressure from the clamps
keeps everything nice and tight. after the glue is dry, i use a black plain to remove the bulk of the ebony stack and then i use a custommade double bearing bit that leaves the ebonyjust proud of the surface. now for one of the more tedious details, the small blocks that gobetween the back rails. each piece is beveled and custom fit to the appropriate location
but it's all worth it whenyou see the final pattern. now it's time to installthe corner brackets. they're held to oneanother with a small dell, the same type of dell is used to connect them to the chair leg and a little pencil duston the end of the dell helps me transfer thelocation directly to the leg. glue is all that's needed to connect the brackets to the rail.
now it's ebony plug time. each plug is pillowed overand polished from a long bar and then cut to size by hand. each plug is theninstalled with yellow glue. the back slack gets a few plugs too only these are made from walnut. as you can see, doing the plugs alone can take some serious time. the finish i'm using is lacquer
and i decided not touse dye on this piece. i think the naturallook of the sapele wood is going to be quite beautiful. i start by spraying the undersides so that i can reach all ofthose nooks and crannies, and then i flip the chair over and focus on the most important and most visible surfaces last. well, the lacquer is dry
and the finish came out pretty nice and if you take a look down here you could see that i stilldon't have a place to sit. what i'm going to do is workwith the local upholster to get a nice drop-in cushion put in here and normally i'd experimentwith that stuff on my own but this is not the kind of project i want to experiment with. i want to make sure that seat looks
just as good as therest of the piece does. whenever i come homefrom a woodworking class, i like to reflect upon what i've learned and not just individual techniques but really the big picture stuff. on a project like this, what it did for me was it ripped the veiloff a chair building. in the past, i would lookat complex chair designs and really have no idea
how i would start that sort of project. i couldn't reverse engineer it in my mind but by seeing a project gotogether from start to finish that's as complex as this one, a lot of those other chair designs look a lot simpler to me now. i look at them and say, "you know what," "if i sat down i probablycould reverse engineer this" "and figure out how to build it."
that's an incredibly valuable thing. of course paying for this class, you really do have to think about the value proposition there. yeah, i learned how to build this chair and i brought this chair home. that in of itself could beworthy asking price, right? for me, the biggerpicture take home lesson is what i really paid for.
the ability to build chairs and not necessarily be afraid of them because ultimately and i've said this in the past many times, everything in woodworkingis just a series of steps. some people notice stepsand some people don't. that's why you take a class like this because it's a shortcut, it's a way to learn that series of steps
so that you too can put that in your woodworking box of tricks and pull it out when you need to, right. it's a very quick way toprogress in your woodworking and really raise yourgame a little bit, right. if you have the opportunityto take classes, i know they're not cheapbut they truly are worth it. do your research, go to a good school, get a good instructor
and i don't think you'llregret it, all right. thanks for watching everyone. i hope you enjoyed seeingthe blacker house chair go together. i know i enjoyed making it and well, i wish i could sit in it but we'll have to waita while for that, right. thanks for watching.